eBook
How to Tackle the Top 3 Challenges with Materials and SAP® Product Data
If you’re running your manufacturing operations using an SAP ERP system you know there’s a mountain of master data behind each product.
Creating and maintaining all that data is a real challenge for many large manufacturers where manual, error-prone processes are still commonplace—slowing down business and causing costly downstream errors—a situation that is no longer acceptable in an increasingly competitive, fast-paced marketplace.
If you’re charged with improving how your business handles materials and SAP product data processes, this eBook is for you. You’ll come away with practical tips on how to tackle the top 3 product data challenges in your manufacturing processes and real-world examples of the results you can achieve by deploying smart, fit-for-purpose automation solutions.
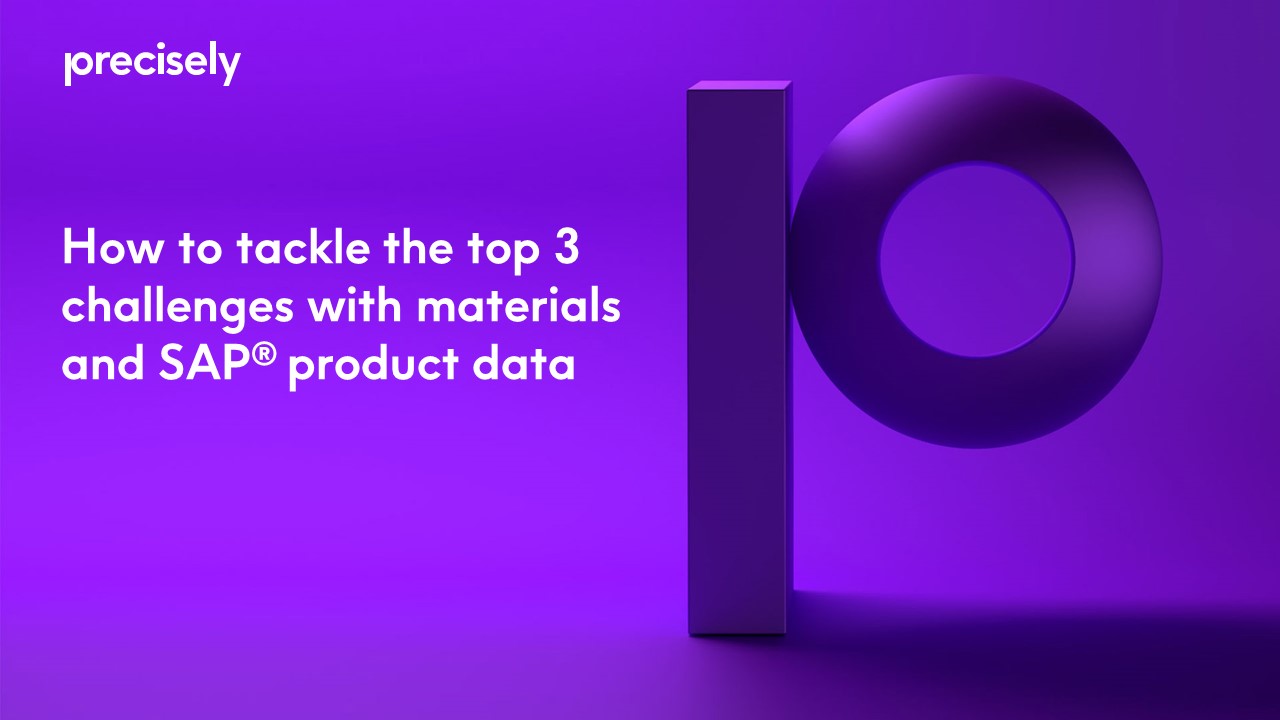
It’s more than just materials
Before we get into how to tackle your biggest challenges with SAP product data, it’s important to note that materials, while the largest and most complex data object involved in manufacturing, is not the only data you need to create and manage—far from it.
Yet, many data management tools are designed only to address materials, are time-consuming and expensive to deploy, and require specialized IT programming skills. To make the biggest impact on your manufacturing processes you need to think about how to apply automation to all your product data and recruit the people in the business who know the processes and data the best to help.
The number of process steps that one food and beverage manufacturer needs to execute after creating a finished good to manufacture and ship the product. Many of these steps require additional functional master data to be created.
Just a few of the typical SAP ERP data objects needed to manufacture and sell products. Data collection processes and elements vary based on whether materials are made or bought.
Challenge 1:
Create and maintain masses of product data
One of the biggest challenges we hear from our customers revolves around the mass creation and maintenance of all that ERP product data.
Organizational changes like mergers and acquisitions can drive the need to create a mass of records in a short timeframe, and business-as-usual events like a simple ingredient change can affect thousands of records.
One solution to get the work done is to ask the already overloaded SAP IT team to develop custom programs to move the data—which can be a slow and frustrating process for the business.
Or worse yet, people in the data team or the business enter the data manually via the SAP GUI—a painfully slow, error-prone and demoralizing exercise.
Solution:
Speed through mass creation and maintenance tasks with Excel
One way to stay on top of your mountain of data maintenance tasks is to use Excel-based solutions that exchange data with SAP in the background—eliminating data entry via the SAP GUI.
Precisely Automate empowers people in the business, like SAP analysts, SAP super users, or master data professionals to build these SAP-enabled Excel workbooks with a simple ‘record, map, run’ process.
People in the business use the workbooks to create or change thousands of records in a matter of minutes and can validate and standardize data along the way to improve data quality. Not only does productivity soar, but morale improves, and people have more time for higher-value tasks.
SAP T-Code | Avg. Time Savings |
---|---|
MM01 / 02 – Create / Change Material | 89% / 77% |
ME11 / 12 – Create / Change Purchasing Info Record | 86% / 83% |
CS01 / 02 – Create / Change Material Bill of Material | 93% / 83% |
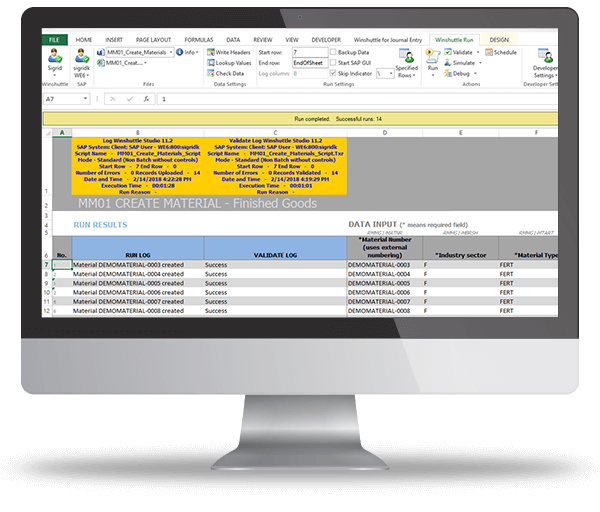
“It’s not just about saving time and achieving greater accuracy. Those are wonderful things, yes. But when people can eliminate mundane tasks and add greater value to the business, their job satisfaction increases.”
SAP Professional Pharmascience Inc.
Success story:
Dorman speeds through product data changes
Dorman is a leading US aftermarket automotive supplier who designs, packages and markets over 150,000 different SKUs. This rapidly growing company has five plants and a high level of master data complexity.
The company needed to change the status of a subset of their materials from manufactured to kitted—a process that involves blocking materials, querying open sales orders and canceling applicable lines, and updating the material master, BoMs and routings. Once the necessary changes are made, the revised order lines are added back into the sales orders.
The IT team at Dorman had been using LSMW for mass data movement but wanted a solution that was easy to use for business teams. They chose Automate Studio and built Excel-based solutions that exchanged data with SAP in the background— eliminating data entry from the SAP GUI and reducing process time from 60 to 5 hours per 100 materials.
This new approach minimized business disruption, and because data is validated at point of entry, data quality is also improved.
Challenge 2:
Slow, manual, product launch processes
According to our recent survey of SAP manufacturing professionals over 74% of respondents feel under pressure to reduce product launch cycles and expect launch volume to increase.
Other key findings:
“Given the disruptive forces at play, competing and achieving new growth will demand manufacturers to innovate new products and adapt business models at a faster pace and on a larger scale than ever before.”
KPMG U.S. CEO Outlook
So, what’s slowing things down?
Our survey confirmed what we already suspected from our customer interactions in this space over the past few years—the majority are still using manual methods for their product launches, mostly spreadsheets and email but paper forms were also commonly used.
Many of the processes that survey respondents automated were done using ‘home-grown’ tools, which are often time-consuming and expensive to change—if they can be changed at all.
“75% of manufacturers report that 15% or more of their product portfolio is updated each year as a result of changes to packaging, ingredients, marketing claims, regulatory compliance and so on.”
Consumer Goods Technology and Gladson
It’s more than just one launch process
If you’ve been involved in SAP product launches for a while, you know that there’s not just one launch process you need to optimize. The data collection requirements and process steps for launching a net new product are very different from making a packaging change or swapping out an ingredient or component.
Regional, product line or plant differences further add to the complexity and make it tough to know where to start when it comes to applying automation.
There is no ‘one size fits all’ when it comes to product launch processes. You need a flexible automation platform that can handle any launch type and the data complexity that comes along with it.
“Consumer preferences are changing at a pace that is unprecedented. Driving that change are millennials, who are looking for products that offer health, transparency, convenience, sustainability and especially experience.”
Cyrille Filott Global Strategist for Consumer Food Rabobank
Solution:
Digitize and accelerate any launch type with one holistic solution
With Automate Evolve’s New Product Introduction (NPI) solution you can digitize any launch type, reducing cycle times by 50% or more. This holistic solution enables you to not just speed up the collection and posting of your SAP product data but also helps you manage critical tasks like artwork changes or sourcing new vendors.
More than just software, our NPI solution includes pre-built content, recommendations based on industry best practices, and expert professional services—all designed to help you rapidly transform all your launch processes.
“With the Precisely Automate platform, we can accomplish the same task much more rapidly. That means getting to market faster—and that’s a massive benefit for us.”
Director of Business Applications Pharmascience Inc.
Digitize at a pace that makes sense for your business
Automate Evolve’s NPI solution is a modular product launch platform, enabling you to digitize your processes according to your business priorities.
Whether you start by automating your process for a packaging change, or dive into digitizing the launch of a net new product, you can rest assured that your solution can expand in the future and be easily modified to keep pace with your changing business.
Challenge 3:
Poor product data quality and costly downstream errors
Thousands of fields across scores of SAP data objects combined with manual, ungoverned data entry practices add up to downstream errors that can cost millions and do irreparable brand damage.
A simple mistake in the Unit of Measure can lead to trucks being overloaded and turned around at state borders or even fines from retailers. An incorrect storage location can cause expensive materials to be scrapped, and one incorrect line item in a BoM can jeopardize product quality.
The examples are endless, and the costs to a business are real.
“It costs about $1 to verify a record as it is entered, about $10 to fix it later, and $100 if nothing is done, as the ramifications of the mistakes are felt over and over again.”
SiriusDecisions 1-10-100 rule by W. Edwards Deming
Solution:
Get data right the first time and keep it right
What if you could implement solutions that prevent bad data from getting into SAP in the first place and help your business teams quickly clean up any existing bad data?
Whether you roll out an Excel-based or forms and workflow solution with Precisely Automate, there’s a lot you can do to build in data guardrails and procedures to improve data quality and ensure compliance with your internal business rules and external regulations.
“The Precisely Automate platform allows you so much flexibility to build in data governance, and route correctly to your business users. It provides business ownership capabilities that make the process very simple and allows users to easily get the work done on time.”
Data Integrity Manager Kellogg
Real-world examples of data stewardship in action
Business Issue | Precisely Automate Data Steward Capability | Precisely Automate Solution Example |
Lots of duplicate vendor records in SAP causing a host of downstream problems. | Search for duplicates | Give people an easy way to check for to see if a vendor exists via a web form that supports multiple search criteria. |
People don’t always know SAP code values for product hierarchy when creating new materials. | SAP F4 lookups | Integrate SAP F4 lookup functionality for product hierarchy into forms-or Excel-based solutions to make it easier to choose the right code based on the product name. |
Business users are putting the incorrect weight unit by mistake when creating new materials. | Restrict field values | Restrict the weight unit choices based on plant location. For example, a plant in Europe would only show metric values, and a plant in the US would only show imperial values. |
Fields are often left out when creating new materials. | Required fields | Make fields required in your materials create web form solution, without going through the pain of making those fields required in SAP. |
Business users are making typos when entering the material number in the component field when creating a new BoM. | Live SAP validation | Give business users the ability to check they have a valid material number via an Excel or forms-based solution, before attempting to post the data into SAP or sending the data to the next participant in the workflow. |
People are wasting time understanding what data they need to supply and where it goes when creating a new material or editing someone else’s data. | Role-based views | Route a web form to users that only shows the fields that apply to their job role via an automated workflow when creating a new material. This will speed up data collection and prevent data being accidentally overwritten. |
Business users are not following the correct format for material description. | Field value rule | Set business rules in a web form to build the material description automatically by concatenating key fields in the material master record. |
Incorrect values for purchasing group and MRP type are entered when creating certain material types. | Smart form logic | Use form logic in the web form used to create new materials to populate the corresponding purchasing group and MRP type based on the material group chosen by the business user. |
Make an impact on all your master data and business processes
Precisely Automate enables you to make an impact across all your SAP master data—materials, vendor, finance, plant maintenance, HR, etc.—and not just on the top-level objects, but on any master data records across the business.
We can also enable you to speed up and improve data quality for transactional tasks such as invoicing, journal entries and sales orders.
Be more agile with Automate Evolve, a flexible, extensible solution architecture.
“The Precisely Automate platform helps us keep up with intense business demand without overwhelming our business users or our IT support staff. I honestly don’t know how we would manage without it.”
General Manager Alpina Savoie