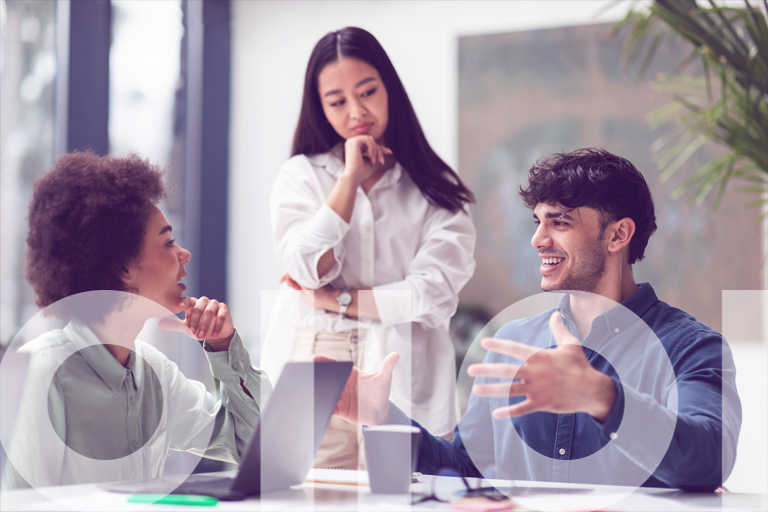
Material Master Data 101: Challenges and Solutions
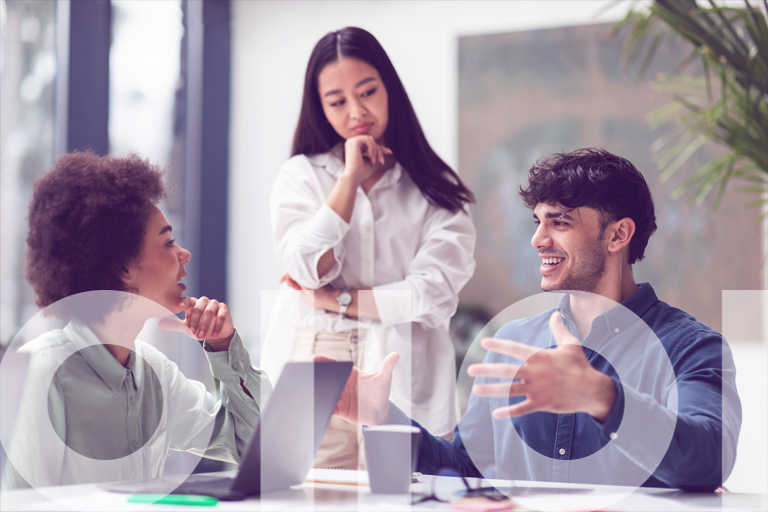
The manufacturing processes you manage in SAP ERP systems require vast amounts of interdependent data. Material master data is one of the crucial pieces that areas throughout an organization rely on for successful operations.
However, manual material data management often comes with many errors and great risks for your business. The good news? Automation can be a game-changer – solving your biggest challenges and unlocking new opportunities.
Let’s dive into the basics of material master data, common challenges of manual management, and how automation helps you overcome those barriers.
What is Material Master Data in SAP?
Let’s start by defining material master data.
Material master data is a comprehensive set of data describing a specific material’s characteristics and attributes. It acts as a central hub for data on the various materials throughout your organization – like raw materials, finished goods, and components.
This data in the material master (SAP mm) provides essential details about your materials, including:
- description
- classification
- dimensions
- unit of measure
- pricing
With insights into elements like these, it’s easy to see why material master data is so critical to get right – areas throughout your organization rely on this information, and it’s the foundation of any efficient supply chain and inventory management system.
However, large organizations that are still using manual, error-prone processes to manage materials and SAP product data processes know that creating and maintaining all that data is a real challenge.
In the dynamic world of product manufacturing and its associated processes, you need speed, agility, and data quality to stay competitive – but it’s easier said than done.
What are the Challenges of Managing Material Master Data?
The materials domain is often regarded as the most challenging of all master data domains, with the greatest number of stakeholders, users, views, and data elements. It also has a direct relationship to business interruptions that can cause a severe impact.
To minimize disruptions and ensure efficient operations, businesses often need to tackle several common challenges:
Mass creation and maintenance of ERP product data. There’s often a need to create a mass of records in a short timeframe, and business-as-usual events like a simple ingredient change can affect thousands of records.
Organizations often rely on already-overloaded master data teams, or shared service centers, for manual entry via the SAP GUI to get the job done – but this approach is slow, error-prone, and demoralizing.
Poor data quality and downstream errors. Keeping accurate and consistent data across various systems and departments can be daunting. A simple mistake can cost millions. If a Unit of Measure is incorrect, trucks may be overloaded and turned around at state borders; there could be fines from retailers. An incorrect storage location can cause expensive materials to be scrapped. The examples are endless and the consequences are big.
Lack of governance. Clear governance policies and procedures for managing material master data are crucial. Without proper governance, incorrect or uncontrolled material master data can result in:
- incurred fines as a result of noncompliance with regulatory requirements
- reduced margin due to inefficient procurement
- stock shortages
- manufacturing line shutdowns
- excessive inventory costs
Not to mention, if your data maintenance and changes are manually managed, you risk degrading your overall data quality over time, which leads to incorrect decisions and compromised business operations.
If any (or all) of these struggles feel familiar to you, then you’re probably well aware of their broader impacts on the business.
Those include:
- reduced efficiency: inconsistent or complex material master data can slow down processes, leading to wasted time and resources, and a decrease in productivity
- increased costs: inaccurate or incomplete material master data often results in errors, reworks, and additional costs. Let’s say you have incorrect product specifications – this can lead to manufacturing defects or customer dissatisfaction, resulting in hits to your bottom line.
- poor decision-making and missed opportunities: when material master data isn’t accurate or up to date, it can hinder decision-making at various levels of your organization. This creates the potential for flawed planning, ineffective inventory management, and missed market opportunities.
To address these challenges and implement effective data management practices, the key lies in automation.
Why You Need Automated Material Master Data Management
How does automation solve your top material master data challenges and get your processes streamlined for success?
Think about all the time spent on day-to-day manual data creation and maintenance of materials, Bills of Materials (BoMs), routings, and other SAP product data. Automating materials master data means you can digitize and accelerate the creation and maintenance of this data to improve efficiency, compliance, and governance.
To stay on top of your mountain of data maintenance tasks, you can use Excel-based solutions that exchange data with SAP in the background – eliminating data entry via the SAP GUI.
Precisely Automate empowers SAP analysts, SAP super users, and master data professionals to build these SAP-enabled Excel workbooks with a simple “record, map, run” process.
These workbooks help you create or change thousands of records in a matter of minutes and can validate and standardize data along the way to improve data quality. Not only does productivity soar, but morale improves, and people have more time for higher-value tasks.
Take the SAP MM01 t-code (create material), for example. Using our Excel-based Automate Studio solution, users see average time savings of 89%. For MM02 (change material), they see an average of 77% time savings.
With the ability to create or update thousands of records in just minutes, you free up time that can be focused on other valuable business objectives.
And for processes that need managed, automated workflows, you have the option of automating Excel files through the process, or using business-friendly, role-based forms that allow users across your enterprise to enter, manage and review data when and where needed, to deliver faster processes, greater agility, improved data quality and complete process governance.
Automated material master data management brings several benefits that can significantly enhance the efficiency and effectiveness of your business operations:
- Improve efficiency: process data more quickly and accurately to achieve greater overall speed and agility. This increased efficiency allows you to be more responsive to changing market demands while saving valuable time and resources.
- Streamline procurement and order fulfillment processes: with accurate and up-to-date data, you can easily identify the right materials to procure, ensure proper inventory levels, and optimize the order fulfillment process. This improves operational efficiency and enhances customer satisfaction by ensuring timely and accurate deliveries.
- Enhance reporting and analytics: material master data contains critical information that can be used for reporting and analytics purposes. Automated data management systems provide comprehensive and reliable data, allowing you to generate meaningful reports, perform in-depth analyses, and gain valuable insights into your business performance.
Benefits like these and more enable the speed, agility, and data quality you need to gain and maintain a competitive edge. They enable more accurate and confident decision-making – faster.
Watch our Webinar
How to Improve Efficiency with Automating Materials Master Data
In this webinar, we cover must-have tips for automating material master data processes that will save you valuable time and effort.
SAP Automation in Action: Real-World Success Stories
For inspiration in your own journey, here’s a look at how just a few of your peers across industries have deployed automation in their material master data processes to reduce costs, boost efficiency, generate new levels of revenue, and more.
Pactiv Generates Significant Revenue Gains and Improves Productivity with Automate Evolve
Minor changes shouldn’t require major time or effort.
That’s why the master data team at Pactiv, the world’s largest manufacturer and distributor of food packaging and foodservice products, needed help: even small design alterations for individual retailers required a new product creation request (PCR).
Creating a new material master for this was tedious. It meant:
- Multiple-step workflow on multiple screens, across departments
- 28-day completion process for a single PCR
- Major loss of potential revenue
But with Automate Evolve, forms and workflow technology enabled the team to:
- Cut material master creation time in half
- Save $1.3 million in productivity costs
- Increase revenue significantly
Philips Lighting streamlines SAP® material master data creation with Automate Studio
Philips Lighting offers over 25,000 products, and has been managing their product lines with SAP since 2011. IT was responsible for managing this database, and any mass data changes were resource-intensive tasks in ERP.
This process became unmanageable very quickly. Over 40 people were managing between 150 and 500 materials, and the risk of errors, time involved, and energy expended stifled the team’s efficiency and productivity.
To simplify and streamline the data creation and updates en masse in SAP, the organization implemented Automate Studio. The results? The team saved 1,600 hours in just 10 months! They:
- automated daily data extraction into Excel (millions of lines)
- reduced time required to create finished products
- significantly improved error management
Alpina Savoie Rolls Out Automate Studio to Maximize Competitive Advantage at a Low Cost
Alpina Savoie produces and distributes 700 varieties of pasta, couscous, semolina, and polenta throughout France and worldwide. The company is France’s second-largest pasta and couscous producer, and they went live with SAP in 2001.
The company faced a backlog of 100,000 FICO transactions and more than 30,000 product references to maintain in SAP – slowly and manually.
However, the team was able to turn that around with Automate Studio. Automation enabled them to:
- update all 100,000 transactions in two days – instead of an estimated three months
- perform fine business analysis more regularly
- manage complex SAP implementation – without increasing staff
Start Your Automation Journey Today for Bigger Wins Tomorrow
You simply can’t understate the role that material master data plays in ensuring smooth business operations. Automation streamlines your SAP MM processes and helps ensure accurate, up-to-date data so you can improve efficiency, reduce errors, and make informed business decisions that keep you ahead of the competition.
Watch our webinar How to Improve Efficiency with Automating Materials Master Data as we cover must-have tips for automating material master data processes that will save you valuable time and effort. Interested in a full demo – contact us.